Difficulties in the preparation of thermal spray coatings
How to estimate the true porosity in a metallographically prepared spray coating is still up for debate, as metallographic grinding and polishing, if not carried out correctly, can introduce artefacts which are not part of the coating structure.
For example, in metal or metal/ceramic coatings, the softer metal is smeared into pores during grinding and, if not polished properly, can cover up the true porosity. In comparison, ceramic coatings are brittle and particles break out of the surface during grinding. If not polished thoroughly, these particles leave an incorrect impression of high porosity.
In general, common difficulties with preparing thermal spray coatings for metallographic analysis include:
Cutting: Clamping of spray coated workpieces for sectioning can introduce cracks in brittle coatings or compress very soft coatings.
Mounting: Cold mounting resins with high shrinkage can cause damage to coatings with weak adhesion to the substrate; due to the shrinkage gap, the coating is not supported by resin, which can lead to delamination of the coating during grinding and polishing.
Grinding and polishing: Edge-rounding can lead to uneven polishing and subsequent misinterpretation of the coating density. In addition, relief between coating and substrate creates a shadow that can be misinterpreted.

Fig. 1: Ceramic spray coating, insufficiently polished
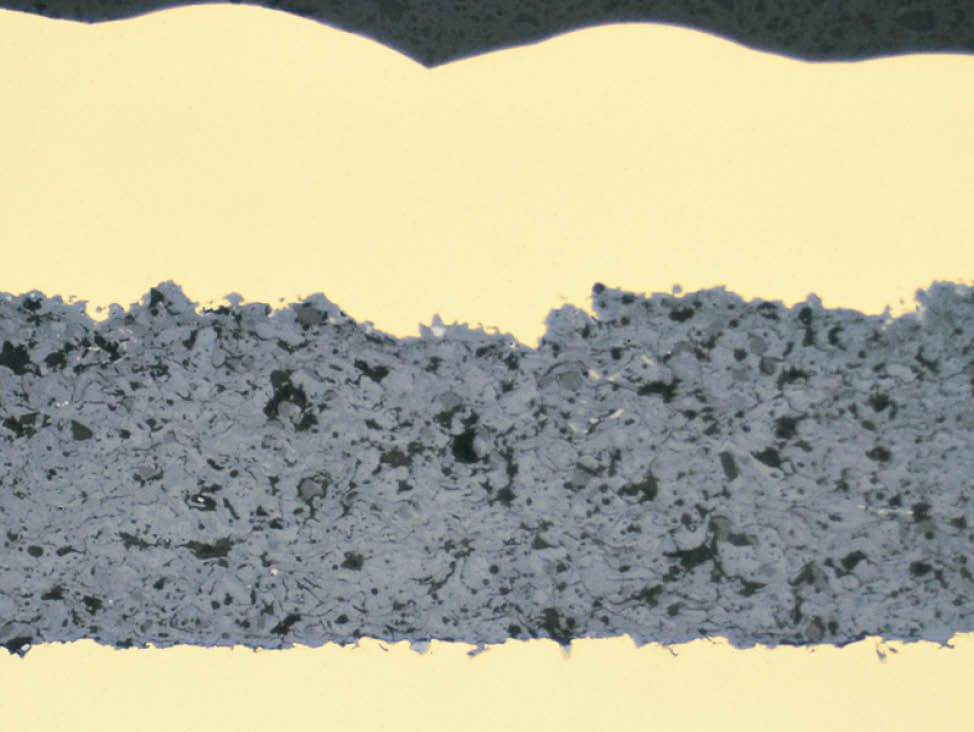
Fig. 2: Same coating as figure 1, but polished correctly

Fig. 3: Edge-rounding can lead to uneven polishing and subsequent misinterpretation of coating density – in this case an incorrect polish suggests less porosity in the middle of the coating
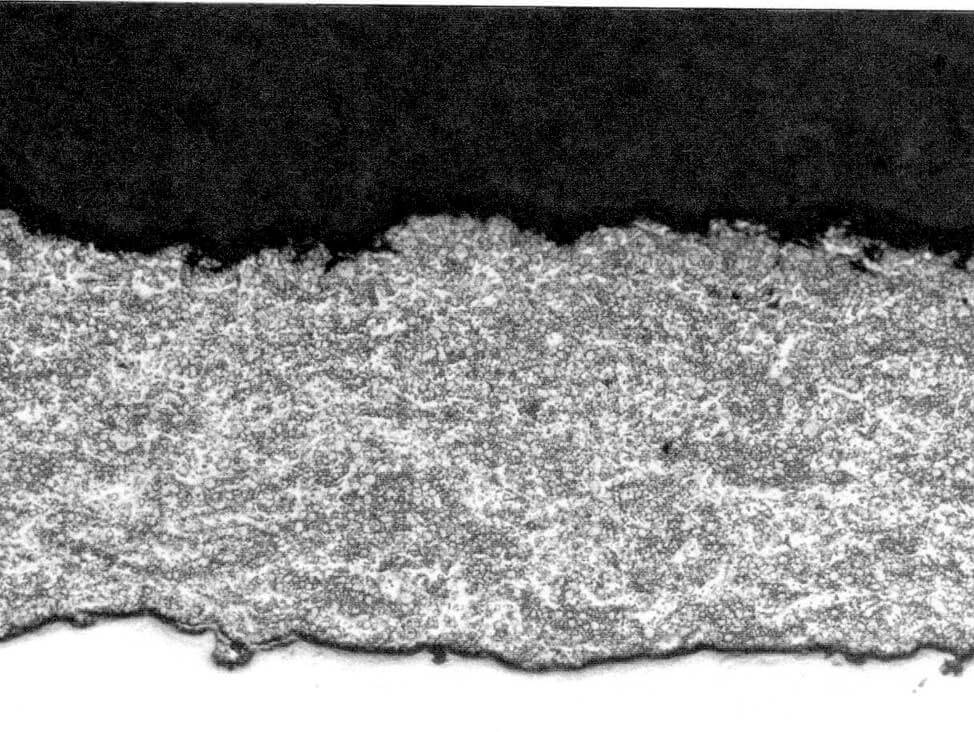
Fig. 4: Relief between coating and substrate creates a shadow that can be misinterpreted – in this case, a WC/Co spray coating with relief polish shows a dark line at resin/coating interface