Copper alloys
There is a large number of copper alloys, with zinc (brass) and tin (bronze) being the most common.
Brass (copper-zinc alloys)
Brasses are copper alloys with 5-45 % zinc. As copper has a high solubility for zinc, the alloys are very homogenous. With increasing zinc content, the reddish copper color changes to the yellow of brass. The brass also becomes harder and easier to machine.
- Brass with less than 28 % zinc is called red brass and is especially suitable for machining
- Alloys up to 37 % zinc consist of α- solid solution and are suitable for cold forming
- From 38 % zinc and upwards, the alloys display a two-phase α-β microstructure, which is suitable for hot forming
By adding aluminum, manganese, iron, nickel, tin or even small amounts of lead, special types of brass with specific chemical or mechanical properties can be produced.
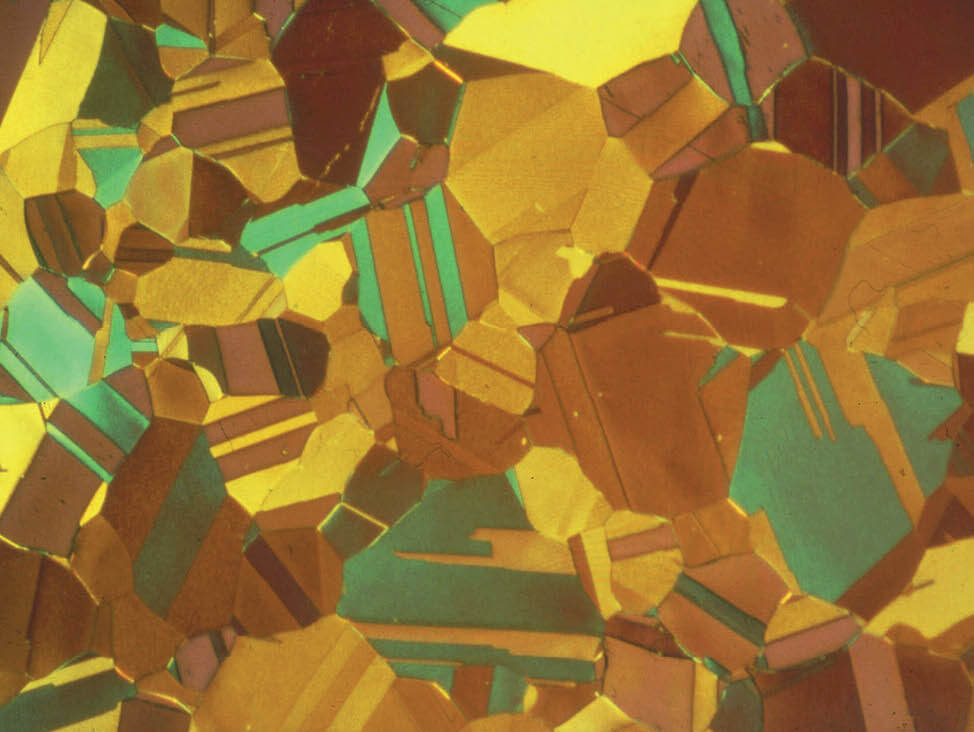
Fig. 4: α- brass, color etched, 200x
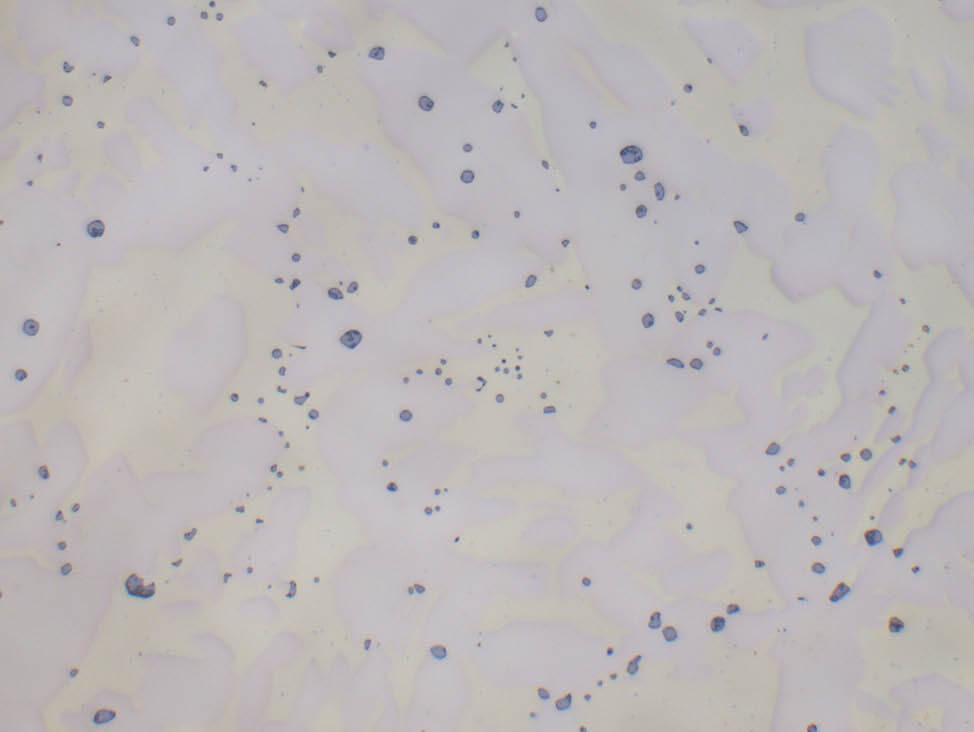
Fig. 5: α-β brass cast (CuZn40Pb2) with grey-blue lead inclusions, unetched, 500x
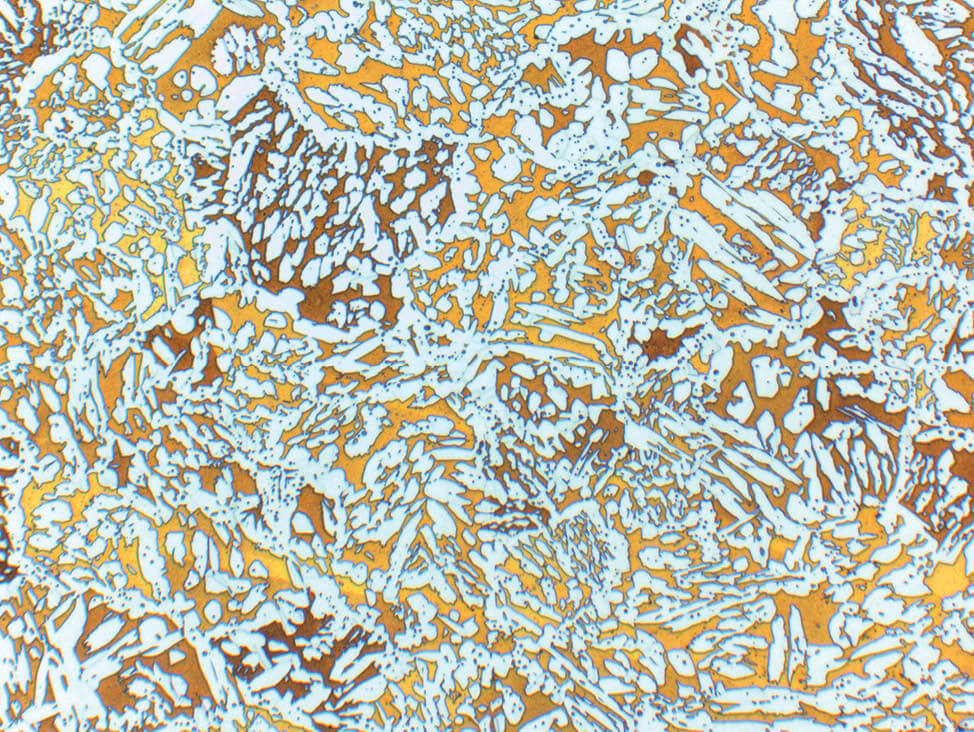
Fig. 6: α-β brass cast, etched according to Klemm, light α- solid solution in dark matrix of β- solid solution, 100x
Bronze (copper-tin alloys)
Bronzes are divided into three types: wrought alloys, cast alloys, and bell casts. Depending on the required properties, small amounts of zinc, phosphorus, lead, nickel or iron can be added.
Some specific brass alloys and their properties |
Gun metal (Cu-Sn-Zn) |
Good corrosion resistance; a low friction coefficient |
Aluminum bronzes (up to 11 % aluminum) |
High strength at elevated temperatures; very good corrosion resistance |
Beryllium bronze |
High strength; high hardness; does not produce sparks when striking or impinging other metals |
Copper-nickel alloys |
Excellent corrosion resistance |
Copper-nickel-zinc alloys (German silver) |
High strength; good corrosion resistance; easy to form |
Fig. 7: Aluminum bronze, color etched according to Klemm, pol. light, 200x